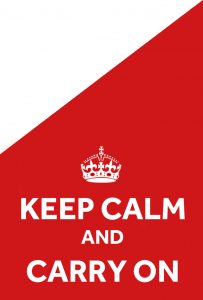
It’s been a strange few weeks.
You should by now by fully aware that we have shifted to remote teaching across MSA including all in-workshop activities from B.15. This has and continues to present new challenges for us all but the school is fully committed to ensuring your degrees are delivered this year as planned.
Due to an IT issue during the huge remote switch-over that has occurred here we have only just been able to access our blog page meaning these updates are a bit later than planned. Anyway, here goes…
Modelmaking From Home
If you cast your mind back to your induction with us one of the key messages has always been to equip yourselves for every eventuality when it comes to modelmaking and this instance demonstrates why that point is so important. Many of you have already expressed disappointment that you may not be able to complete ‘presentation’ models of your projects because you cant access the workshop. This is simply not true.
Modelmaking is a tool for exploration and not exclusively tied to the workshop environment and we strongly believe that you can achieve great results through exploration without the need for great expense or constant workshop access. We can all adapt and we’re here to help you do so.
A presentation model is a representation of your finished idea that is resolved or at least a snapshot of your design work to that date. This doesn’t limit itself to any particular machine, tool or material but takes its ‘presentation’ status from the quality of the design that it portrays and the consideration for the way it is put together. Be resourceful and don’t limit yourself to machines or a single medium as a means of getting your ideas across. Your hand making skills can be just as effective. Be patient and experiment with different soft modelling materials you may have. observe how they work or don’t work to your advantage and present your findings as they are. Mistakes are just steps towards more resolved pieces and should be embraced as being absolutely necessary.
Tutorials to help with Modelmaking from Home
Over the last week and a half we have been running remote tutorials for anyone wanting to produce models from home. These have covered anything to do with this field in terms of theory, technical questions, tools/materials questions and recommendations and general concerns that quite naturally, many of you have.
Thank you to everyone who’s signed up and shared their ideas with us. It’s encouraging to see that you’re willing to adapt to the situation and see what we can come up with.
If you would like to speak with us about any ideas you have or how you might adapt your original plans please get in touch via email or using the Moodle form which can be found on this post on the main announcements page (you need to be logged into Moodle: https://moodle.mmu.ac.uk/mod/forum/discuss.php?d=502741
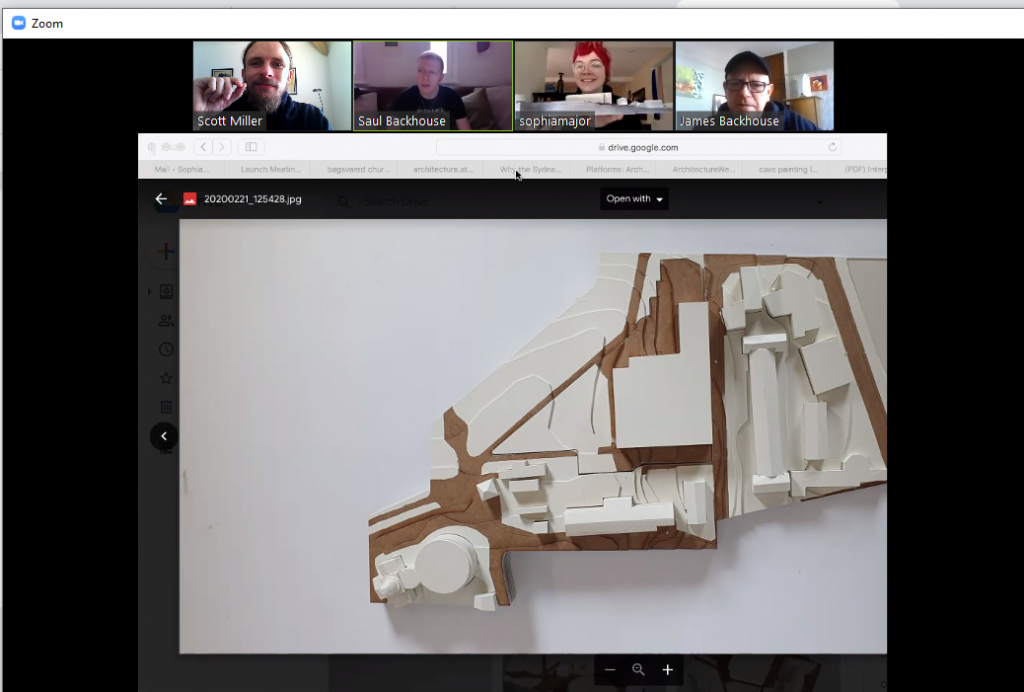
Getting tools/Supplies
A number of you were able to get orders in with 4D before they closed which should be with you in the next week, possibly a little longer internationally depending on the different postal services.
For those who might need tools or materials in the UK Emily Crompton has confirmed that it is still possible to order from Fred Aldous for delivery and that there is a 20% MSA Student Discount. For the discount code please get in touch with us or ask during your tutorials.
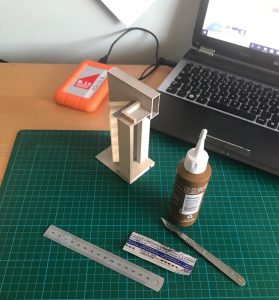
In Other News……
Atelier La Juntana Summer School 2020 Cancelled
For obvious reasons this years International summer school in Northern Spain is now cancelled. We will review the situation in the new academic year with regards any future collaborations with the school. If you had applied and paid any deposits for the course should should have been contacted about a refund. If not then please get in touch with the organisers to make sure you get your deposits back.
B.15:50 events
Before the enforced lockdown we had a number of planned events that would have taken us up to the end of this academic year. Again these have been cancelled for now but we hope to reschedule all events once things are back to a level of normaility.
In the meantime we hope to put out the video footage of our guest lecture from Simona Valeriani of the V&A. Keep an eye out for that.
Annual Modelmaking Awards
We were due to announce plans for this years awards last week but have decided to rethink how these will take place given the change in situation. We will be making an announcement about this in the near future.
There is a lot of uncertainty about the coming months but the main thing is for you to look after yourselves. We’re here if you need any advice and look forward to hearing about your ideas.
Keep making and we’ll be in touch soon,
Jim, Scott & Saul