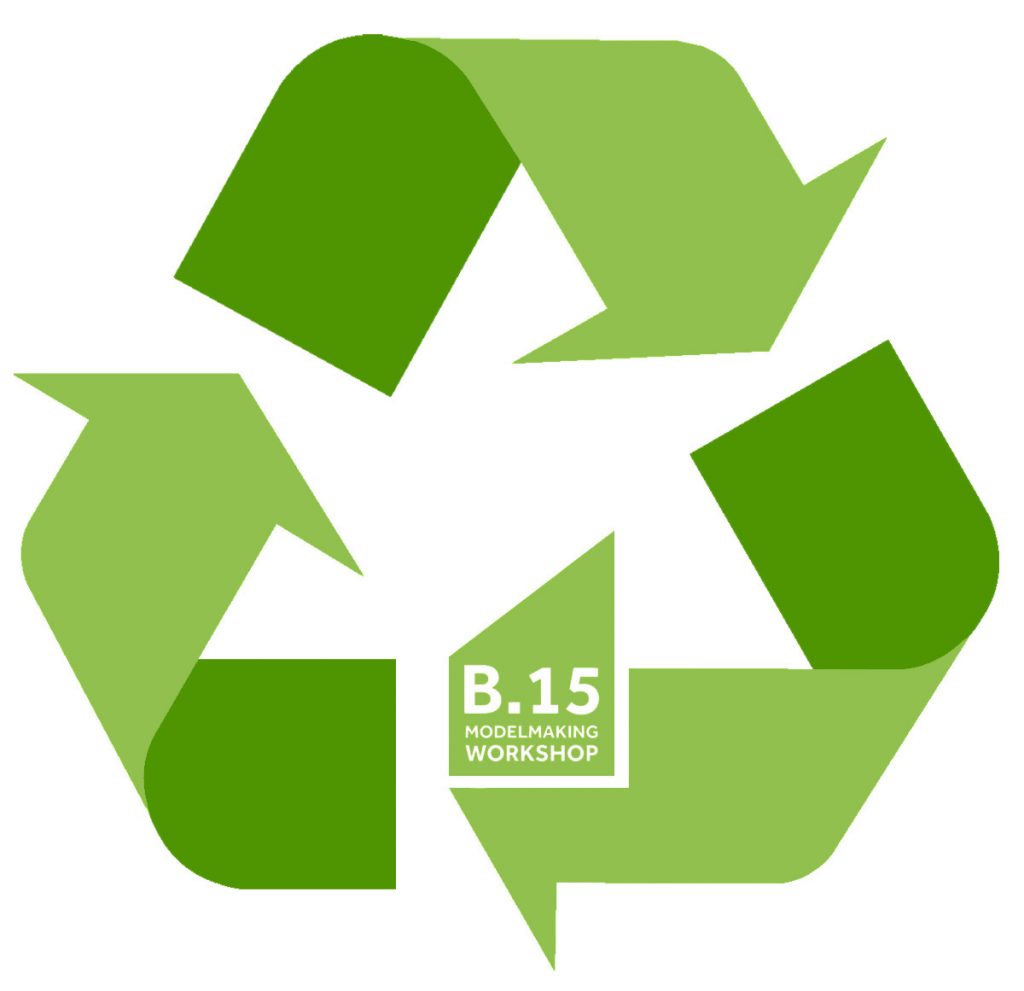
One of the inevitable by-products of a creative environment such as ours is a large amount of material waste. Whilst a certain amount of this is unavoidable we endeavour to reduce as much unnecessary disposal as possible.
As individuals we all need to be more considerate to make a difference to this and every little change can help.
Here’s a few things to think about for this cause and your own and everybody eleses benefit:
Materials Consideration
This is a huge part of your project and should be thought about in great depth in terms of what you are trying to achieve and the potential waste produced from it. For example, When making a contour model consider the amount of unseen sheet material that could be saved by producing each layer as a step down rather than an entire sheet to form each layer. Could you use grey cardboard which is widely recycled instead of sheets of wood? Always check the free recycled materials before using virgin sheets.
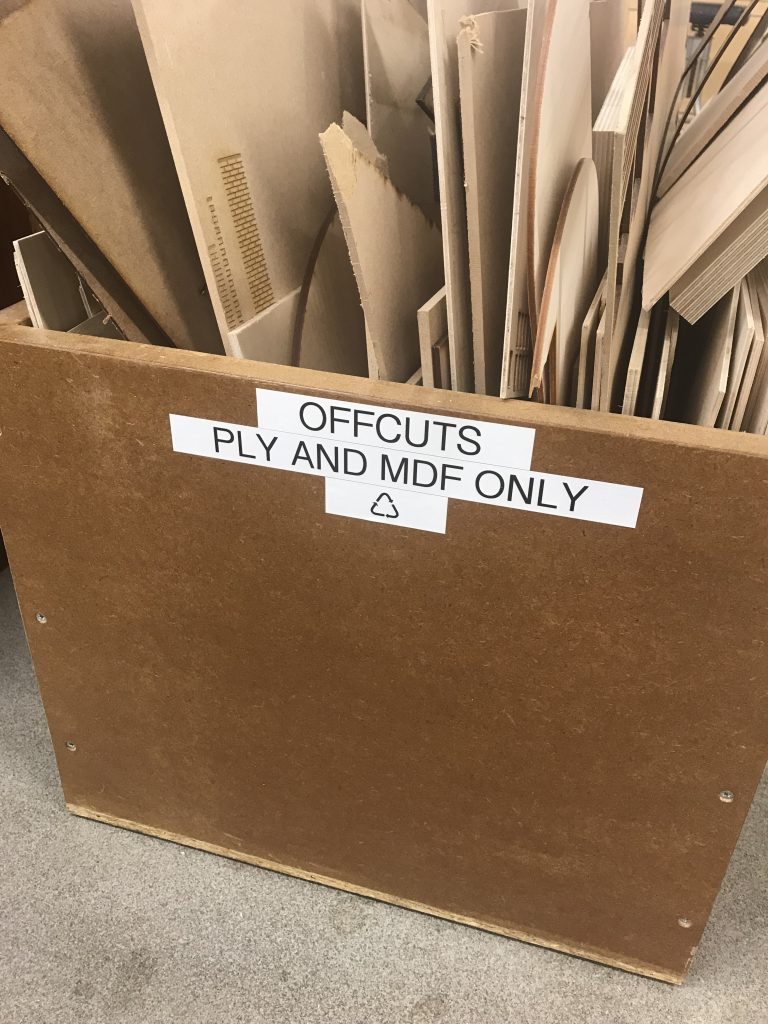
Planning Your Model
Establishing the size and layout of your model can dictate how much material you use. For example if you want to make a laser cut model that measures 900mm x 600mm you will need to use more than a standard laser cut sized sheet (800mm x 450mm) of material to cover the area required. For the sake of using another sheet of material, your money and little visual difference to the end product you should try to work to existing sizes.
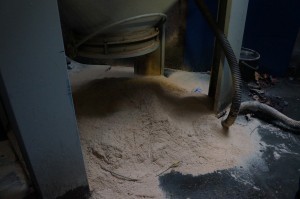
Using Machines Appropriately
This is always a sticking point for students using our workshop as experience of machine use is varied. By thinking about each component you are trying to produce beforehand it is possible to produce the desired shape without unnecessary waste.
For example when using the disk sanders to create a roof pitch we can think about the size of the piece we are working with. If the piece requires taking large volumes of material away then it would be more appropriate to cut the majority of the material away using a band saw before moving to the disk sander to accurately finish the cut. By doing this we are reducing the amount of wear to the disk sanders and the levels of dust in the atmosphere around the workshop.
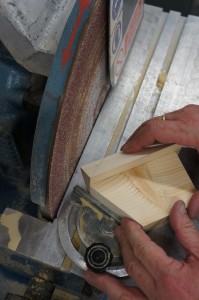
Using Offcuts
With a bit of fore thought it is possible to make virtually anything for next to no cost by utilising off-cuts and unwanted material for others projects. Here in the workshop we have off-cut bins for wood and drawers for cardboard and acrylic of varying sizes and thickness. It is always worth looking at what is available for free to reduce using material and in turn your costs.
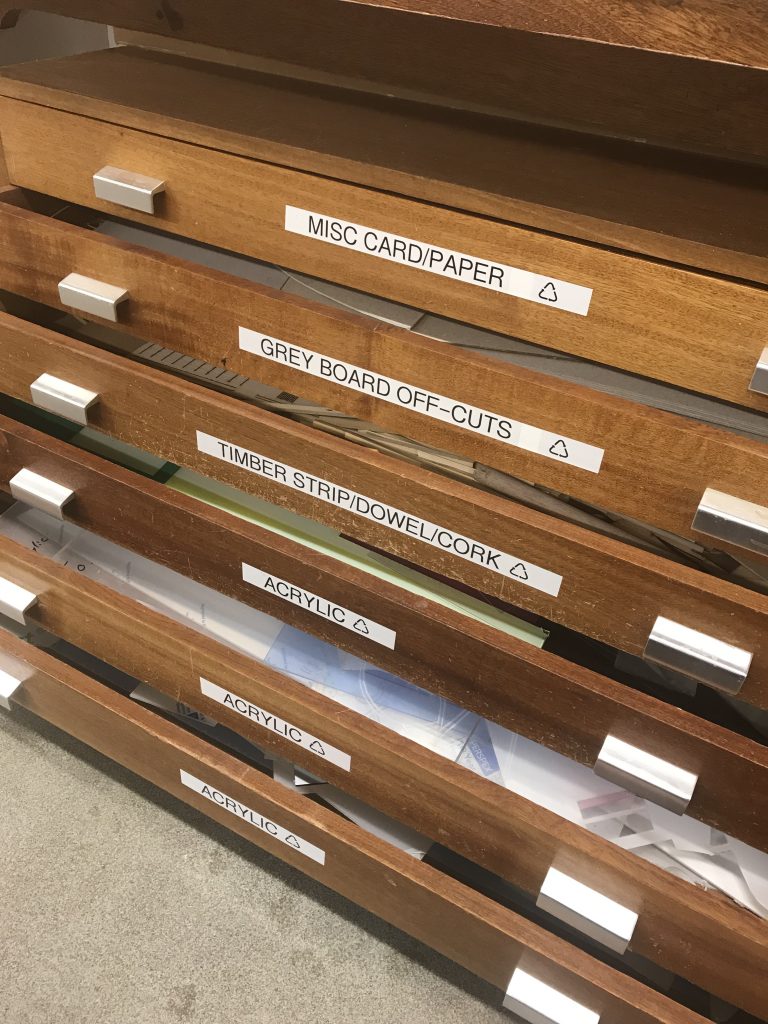
Thanks for taking the time to read.
Scott