“Designed in the 18th century by the artist Giovanni Battista Piranesi (1720-1778), Caffè degli Inglesi in Rome, just moments away from the Spanish Steps, is a prime example of a lost ‘cultural cafè’. Renowned for its eccentric Egyptian style, it was a main hub for British artists visiting the Eternal City. Although it was a key centre for culture and artistry, the café’s design divided opinion. Caffè Degli Inglesi only survived for circa 20 years.
Only two plates etched by Piranesi himself have survived that depict one long and one short internal wall. Because of this, our main challenge was re-imagining the space. As the cafè is long gone and we have no information in regards to the materials, colours, techniques employed, it therefore seems clear that the physical architecture of this space shouldn’t be our main focus, but capturing the lost atmosphere by trying to create a ‘shadow’ of the lost physical space.
When creating a three-dimensional model, it was obvious we needed to depict the two undocumented walls in a way that does not mimic nor assume, but can capture the spirit needed for the café’s re-interpretation. We are therefore suggesting the use of mirrored walls, providing an immersive experience, without compromising the integrity of Piranesi’s unknown original design.
The material choice for the rest of the model was intended to hint towards Piranesi himself’s original metallic plates. The time and expense required in producing real metal plates was soon deemed too unrealistic, therefore an innovative solution was found in aluminium powder mixed with resin to create a metallic, durable cast acrylic sheet. From these they were able to be handled by machines such as the laser cutter in creating the etchings on both sides.
A challenge came in the creation of the vaulted roof, where the material was heated following the etching process and formed around a pre-made mould. The 4 sheets were then filed so that the edges could align as best as possible. Assembly of the model involved super-glue, epoxy resin (made metallic in the same way as the cast sheets to match) and finishing using 3mm self-adhesive lead strips.
We were asked to display the model on a 400x400mm plinth. This was created with a number of feature to help enhance the model, for instance the plinth was created to be 1500mm high in order for the model to be viewed from eye level and allowed the viewer to experience the mirroring of the materials within. The rectangular shape of the model was then rationalised by creating a series of steps at the top of the square plinth, the final step incorporating a step down to fit the model so that the floor plate runs smoothly from outside to inside. The plinth was then painted in a matt white, with a shadow gap creating a neat finish between plinth and floor.” – Vanessa Torri & Daniel Kirkby 2015
Making the Model
For this project it was decided to make the wall thickness 3mm for ease of construction as well as keeping the material use to a minimum. Simple tray moulds were made up using strips of 3mm MDF that were double sided taped down to a base. This aids an easier removal from the mould once the cast has cured.
Note – if it is clear that a lot of the same component are require (in this case resin slabs) that it may be worth making the mould using a silicone to allow repeat casts and easy cast removal. As this project was very much ‘try it and see’ the required moulds were made as needed.
Once the basic mould was complete the surfaces were coated with a barrier coat of Vaseline to prevent the resin penetrating the surface of the MDF when poured.
Metal powders
The use of metal powders in casting allows us to create a lightweight and, when compared to full metal casting, low cost but effective substitute material. The process uses very fine metal powder to coat the surface of a desired cast that can then be polished as if it were cast in the metal in use. In this case Aluminium powder was chosen to emulate lead.
In order to guarantee a good coat of metal powder on the surface of casts the mould should be dusted with the desired powder. The excess powder can be poured from the mould and reused.
Mixing/Pouring Resin
For ease and speed of casting fast-cast- polyurethane resin was used as the stock material for the cast slabs. The resin is usually mixed at a 50/50 ratio but always check the instructions as some brands do vary their instructions on ratio mixing. As we were going for a metallic finish overall metal powder was also mixed into the resin to back up the surface coat already ducted into the mould. As the resin is poured the metal powder particles naturally want to sink to the lowest point so having them in the resin only increases or chances of a successful finish on the face of the cast.
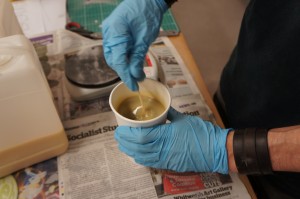
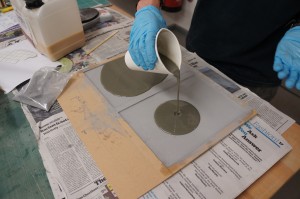
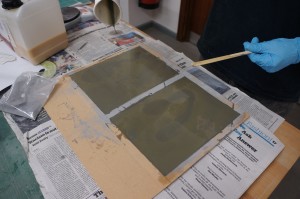
Surface Finishing and Laser Engraving
Once the slabs have poured they can be carefully removed from the mould and all being well will have a dull but flat finish on the down face. Using wire wool the surface can be polished up to the desired shine.
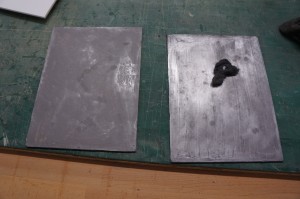
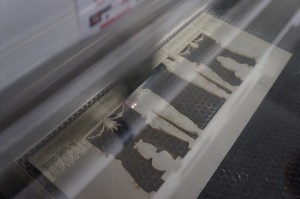
Next up for this project was the engraving of the Piranesi drawings onto the plates. Using the laser cutters Daniel and Vanessa were able to engrave into the polished surface of the plates as well as the back face which would end up being inside the model.
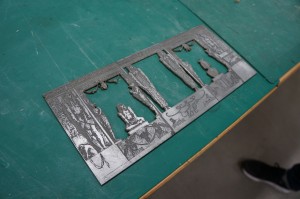
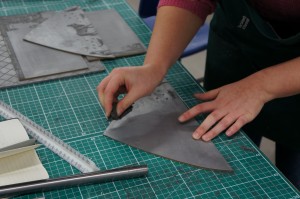
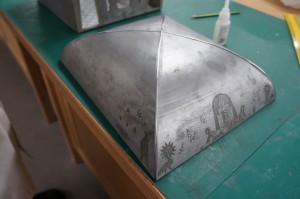
The roof components required heat forming to create its vaulted shape. This shaping occurred after being engraved and cut to shape which required significant time to figure out correctly.
The final detail to be added to the model was lead finishing strip as used on leaded windows. As well as finishing the panel gaps this strip. lent itself to the model design and matched the metallic finish perfectly.
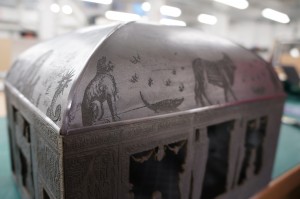
The model will be on display as part of the 5th year ‘Lost Spaces’ workshop display at the end of year show in June.